Building Regulations as They Apply to Roofs-Part L
When the South African National Building Regulations were updated by the Department of Trade and Industry in May 2008, the General Requirement relating to Roofs was changed to incorporate certain safety elements.
For example, instead of simply having to “resist any forces” to which the roof might be subjected to, the regulations now state that “The roof of any building shall be so designed and constructed that it safely sustains any actions which can reasonably be expected to occur and in such a manner that any local damage (including cracking) or deformation do not compromise its functioning”. In simple language, if there is a major wind or some other really horrible weather conditions (God forbid), the roofs of our homes are expected to be able to stay on the house and protect us from the elements without themselves being damaged.
Instead of simply being “durable and waterproof”, roofs are expected to be “durable” and should not allow “the penetration of rainwater or any other surface water to its interior”.
As previously, roofs must “not allow the accumulation of any water” (but not simply rainwater, which was the limit of the old building regulations) “upon its surface”. In addition, the roof should be “adequately anchored against wind uplift” which was not covered in the previous edition of the regs.
Lastly, the General Requirements specify (as they did previously), that the roof should be designed “as part of a roof and ceiling assembly” and should provide “adequate height in any room immediately below such assembly”. This last one, though, is open to interpretation as not all roofs incorporate ceilings as such.
The South African National Standard for Roofs
While the legislation changed in 2008, it was only in 2011 that Part L: Roofs was published by the SABS. And the changes are substantial. It’s not so much that they’ve changed, but rather that the guidelines are now much more comprehensive and useful.
General Rules for the Construction of Roofs
As with most of the National Building Regulations, those that apply to roofs relate to SANS other than the one specific to that particular element. For instance, where any roof is to be supported on the wall of a building as described in the relevant section of Part K: Walls, the roof MUST be constructed in accordance with the rules laid out by the relevant SANS (in this case 10400). In addition, the new SANS remind designers and builders that other sections are also vitally important when it comes to roof design, including Part A: General principles and requirements; Part B: Structural design; Part C: Dimensions; Part R: Stormwater disposal; Part T: Fire protection; and Part V: Space heating.
Of course they are. Any qualified designer knows that every one of the SANS that form part of 10400 needs to be considered as a whole. It’s just because the different new sections were published over a period of years that has made it more of a challenge for many.
Since anybody building a house MUST either BE a “competent person” in terms of the regulations, or must EMPLOY a “competent person” to put in plans and oversee the building operation, either you or the person you employ should purchase the updated section of SANS 10400 Part L Roofs from the SABS to double-check details and specifications. Also be acutely aware that circumstances vary from site to site.
There are several South African National Standards (SANS) that relate to roof timbers, all of which must be complied with when roof trusses and other roofing elements are constructed. In addition there are standards that relate to roof coverings and other elements. They include:
- SANS 542, Concrete roofing tiles
- SANS 1288, Preservative-treated timber
- SANS 1460, Laminated timber (gluglam)
- SANS 1701-1, Sawn eucalyptus timber – Part 1: Proof-graded structural timber
- SANS 1701-2, Sawn eucalyptus timber – Part 2: Brandering and battens
- SANS 1783-2, Sawn softwood timber – Part 2: Stress-graded structural timber and timber for frame wall construction
- SANS 1783-4, Sawn softwood timber – Part 4: Brandering and battens
- SANS 2001-CT2, Construction works Part CT2: Structural timberwork (roofing)
- SANS 10407, Thatched roof construction
You’ll find the full list in Part L of SANS 10400 (or check with an SABS librarian for the relevant information).
Basic Requirements
Roof design depends on a number of factors including the type of covering you are going to use, and the span over which the roof structure is to be supported. More often than not, the roof structure is assembled from a series of roof trusses. These rest on wooden wall plates, and are designed to span the walls of the house. They will be either nailed or bolted together on site, or delivered to site on order by a specialist truss manufacturer.

The trusses themselves are made up of rafters, tie beams, posts and struts, all of which are assembled according to a specific design. The illustrations above shows some of the most usual configurations. The new regulations have simple line drawings for:
- Four-bay Howe truss with a maximum clear span of 6 m (the same as centre right above)
- Six-bay Howe truss with a maximum clear span of 8 m (called a King Post Truss above)
- Two-bay mono pitched Howe truss with a maximum clear span of 3 m
- Three-bay mono pitched Howe truss with a maximum clear span of 4 m
The regulations also state that no member of any truss should have a length that is greater than 60 times its smallest dimension.
The basic requirements shown in the table below, apply to Howe-type trusses as listed above. There are some additional tables mentioned below.
MAXIMUM TRUSS SPANS FOR RAFTER AND TIE-BEAMS
*a Heel joints should have 2 x M12 bolts per joint with 40 mm washers at each end
*b All timber members should have a thickness of 38 mm or 36 mm if the timber is planed
*c 38 mm x 114 mm Grade 7 members may be substituted for 38 mm x 152 mm Grade 5 material, if required
*d The maximum overhang of a 114 mm top chord or rafter is 600 mm. The top chord or rafter must be increased to 152 mm if the overhand is greater than 600 mm but less than or equal to 900 mm
[TC = top chord; BC = bottom chord; web = cross pieces that tie the structure together]
This table is considerably more useful that the one that was in the previous 1990 edition of the regulations, as not only maximum truss spans are indicated, but also the allowable and recommended pitch of the roof, and the member sizes and grades of timber that are specified in SANS 1783-2.
You will also see that the maximum centre-to-centre spacing of the trusses varies according to the type of roof covering you are going to be using.
Another element that is specified in this table is the type and number of bolts to be used at heel and splice joints (although it must be said that builders often use nails).
A heel joint (mentioned here) is simply an indentation that is cut into a rafter so that the timber can rest on the top plate. Normally this type of joint is about a third of thickness of the rafter.
The new regulations have a number of different tables that specify the maximum clear spans for rafter and/or purlin beams. Specifically for:
- Sawn softwood rafter beams that have a pitch of less than 26 degrees
- Laminated SA pine rafters that support tiled or slated roofs that have a pitch of less than 26 degrees
- Laminated SA pine rafters that support profiled metal or fibre-cement sheeting or metal tiles with a pitch of less than 26 degrees
- Sawn SA pine purlin rafters or purlin beams that support profiled metal or fibre-cement sheeting
- Laminated SA pine purlin rafters or purlin beams that support profiled metal or fibre-cement sheeting
- Gum pole rafters
The timber grades allowable for softwood and all SA pine rafter beams is Grade 5 and Grade 7. Laminated beams should be Grade 5 or higher and should comply with SANS 1460. Where relevant, specifics are shown in the tables for maximum clear spans for sawn softwood beams with a 26 degree pitch below.
Note that the type of roof covering in this table (maximum clear spans for laminated SA pine supporting a tile or slate roof with a 26 degree pitch) is shown in the first column, and the rafter spacing in the other four columns. Also note that the maximum mass of tiles or slates, including battens or purlins, should not be more than 65 kg per square metre.
Note that * indicates the most commonly available sizes. Below is a table for maximum clear spans for laminated SA pine rafter supporting profiled metal or fibre-cement sheeting or metal tiles with a 26 degree pitch
Note that * indicates the most commonly available sizes. Below is a table for maximum clear spans for SA pine purlin rafters or purlin beams supporting profiled metal or fibre-cement sheeting (or metal tiles in the table below) with a 26 degree pitch.
Below is a table for maximum clear spans for gum pole rafters with a pitch above 26 degrees and above 26 degrees.
The maximum mass of the tiles or slates, including battens or purlins, shall not exceed 65 kg per square metre.
In addition to maximum spans, there are also minimum requirements in terms of slope (or pitch) and minimum end laps.
When it comes to thatch roofs, generally the slope should be 45 degrees, except at dormer windows where the slope should only be 35 degrees. The minimum thatch layers and thickness vary depending on the type of grass or reed used for thatching. Fine thatching grass or reed should have a 1.2-2.5 mm stem/butt diameter, and it should be 175 mm thick. Coarse thatching grass or reed should have a 2.5-4 mm mm stem/butt diameter, and it should be 200 mm thick. Water reeds should have a 1-7 mm stem/butt diameter, and a 300 mm layer thickness.
Some Important Factors Regarding Connections
It is vital that roof trusses and other roof framing elements have joints that are accurately cut, securely made and fitted so that the component parts are drawn tightly together. All trussed roofs MUST be provided with approved bracing that prevents any possible buckling of the rafters, tie-beams and long web members. The bracing also needs to keep the trusses in an upright position. Whoever is doing the maths need to be certain that no section of the truss has a length that is greater than 60 times its least (or smallest) dimension.
If rafter construction is used instead of roof trusses, and the roof covering is regular sheeting or tiles (as already mentioned), it is important to accurately assess the parameters for rafter spans and the size and grade of rafters. Please note that if the rafter spacing is not the same as that shown in the table below, intermediate values of maximum rafter spans may be interpolated within the range of values suggested for relevant timber grades.
When constructing a roof framework, the rule of thumb is that any purlin should have a minimum nominal depth and width of 76 mm or 50 mm, and max centre-to-centre spacing between the purlins ought to be 1,2 m. Joints between purlins next to one another should be staggered. But the tables that follow are a lot more specific.
All roof trusses, rafters and beams that are supported by a brick or concrete block (or even a stone) wall must be securely fastened to the wall using galvanized steel strapping or galvanized steel wire that complies with the National Building Regulations. It is also important that fasteners are resistant to corrosion.
If you order factory-manufactured trusses that are made with metal plate connectors, they may not comply directly with the requirements of the various tables in the SANS. But a “competent person“ will be able to tell you whether they meet the requirements of the regulations. If you buy from a reputable company you can rest assured that they will be absolutely fine.
Remember that the National Building Regulations are not prescriptive. But because they were established as a guide to MINIMUM standards, you must never ignore them.
Pole Construction
You will notice that the last table above is for gum pole rafters. Pole construction is another new addition to the NBR SANS.
If this method of construction is used, softwood poles must comply with SANS 457-2 and hardwood poles must comply with SANS 457-3, and ALL poles must be treated in accordance with the requirements of SANS 10005. If they have cracked or the end are plot within a space that is equal to the diameter of the pole, they MUST NOT BE USED. This is simply a structural issue.
If poles are sawn or reshaped at the ends, any of the exposed ends must be treated with a Class W preservative. It is also necessary to cover at least 35% of the surface area of the end with a new nail plate to prevent or at least minimize cracking.
Thatched roof construction – which utilizes pole structures – is also mentioned, though there are additional standards that need to be referred to.
For thatched roofs, laths must have a minimum diameter of 25 mm and they must comply with the requirements of SANS 1288. Spacing must be done according to SANS 10407. If a thatched roof is constructed with gables, without hips, valleys or dormer windows, it must have a pitch of 45 degrees, and a clear span that is no more than 6 m. Construction must also be in accordance with SANS 10407 and with additional specification in SANS 10400-L that are shown in the form of drawings and a table. You will need to either buy the standard or visit an SABS library to access these. In the drawings, specifications for rafters state that if the poles are 100 mm to 125 mm in diameter, then the truss clear spans may not be greater than 4 m. If the poles are 125 mm to 150 mm in diameter, then the spans may be more than 4 m but not greater than 6 m.
Protection from the Elements
There are other factors that relate to fire resistance an combustibility, and waterproofing – which of course has to cover (excuse the pun) flashing and flat roofs!
- Fire resistance and combustibility relate to light fittings and any other components that penetrate the ceiling, as well as the non-combustibility of “such assemblies”. No part of any roof or ceiling that is made of wood or any other “combustible” material is permitted to pass through any separating element of a building.
- Waterproofing refers mainly to runoff water from the roof … and therefore relates directly to the slope of the roof. This, in turn, is totally reliant on the roof covering used. SANS 10400 has specs on minimum roof slopes and sheet end laps. The new regs include a number of invaluable drawings that show principal waterproofing details including parapet wall waterproofing on balconies; where it is required against a solid brick wall; where it is required against a concrete balustrade wall on a balcony or against an ordinary concrete wall; and various other balcony details. Additional waterproofing details include a stepped DPC in a cavity wall; tanking against a cavity wall; waterproofing under timber and aluminum door frames; and waterproofing at a shower base.
- Flashing, which is used to stop leaks coming in from around chimneys and other “projections”.
- Flat roofs are an issue all on their own! For instance, flat roofs are not actually flat, they MUST have a fall of about 1:50.
Part L of the updated national building regulations (published in 2011) also include new sections on roof coverings and waterproofing systems for pitched roofs, and drainage and waterproofing of flat roofs.
>
Hi, I have built a small house in George and have a Mitec designed roof with concrete tiles. I have used the hoop iron method of fixing the trusses to the wall (6 tiers). The roof was inspected and certified by an ITC inspector as being erected correctly. The NHBRC refuses to accept this certificate and maintains the trusses are not correctly affixed. They require another technique where a roof anchor is concreted in place in the cavity. I maintain my method is acceptable. Do you agree?
Are you registered with the NHBRC?
Yes, this is a late enrollment.
ITC inspector is right there are numerous methods of fixing and galv. wire built into the brick’s it’s must commonly used trough RSA as well as roll bolt into the wall with hoop iron to hold the trusses down, the problem comes where there is a cavity wall they would want both brick layers to hold down the trusses(distributed load) instead of just one layer of brick wall, with wind uplift in the coastal regions being such a big problem a single skin wall(one 110mm brick layer) is not sufficient there is a big chance that the one brick layer might just pull lose, structurally a single brick layer is not strong enough. might need to consider strapping from the other side as well to resolve the problem the quickest.
Funny thing this info is so old and out dated.
For instance you do not get grade 4, 6, 8 timber only grade 5 and grade 7 timber.
And also 1400mm C/C for sheeting with a timber construction you will need to use steel purlins, for timber purlins is too weak to span that distance. That is why light weight steel building systems is becoming so popular now for larger span capabilities and bigger truss spacing. not to mention the other advantages.
I have a very low pitched roof, about 20 degrees. It has concrete tiles but the trusses are first covered with shutter board and then waterproofing. the tiles have then been fitted on top of this. Does this type of construction conform to building regulations as I have been given conflicting answers. Some say the pitch is too low for tiles, and it is irrelevant that the shutter and waterproofing has been applied whilst others say it is perfect because of the extra waterproofing? Please can someone advise what the law states.
Brandon,
1. Any roof with a pitch of less than 15 degrees is considered to be flat.
2. Concrete tiles are generally laid on trusses that have a pitch of at least 26 degrees.
But this is not law. Have a look at http://sans10400.co.za/roofs/ to see more about what the NBR and SANS 10400-L say.
Basically there are various different classes of roof covering (clay and concrete are Class B), and the SANS gives guidelines for truss spans for rafters and tie-beam sizes. I believe that as long as the pitch is between 17 and 35 degrees, Class B coverings are fine.
I hope that helps.
I will check these specs Tiaan and update them if I can.
Good day
Im building a small get away house for weekend about 100sqm.
I want to fit a flat roof sink or tiles what must the cinstruction look like and the slope of the roof
Regards
My book, Owner Building in South Africa gives a detailed list standard specs for the pitch (slope) of roofs. Requirements for roof sheeting (e.g. zinc) and tiled roofs are totally different. The materials used to manufacture tiles also affect minimum pitch. These materials also affect the maximum spring of roof trusses, purlin or batten sizes and the spacing of battens and purlins. Generally you can have a much flatter roof with sheeting than with tiles, because it is easier to achieve the required run-off for rain water.
Bear in mind that a “flat” roof isn’t totally flat; most have a pitch of about 5 degrees.
The builder installed new ceiling before finishing the roof, resulting in the ceilings getting wet, they have to poke wholes in the ceiling to let the water through, what is the regulations regaring ceilings?
I don’t think this is an issue about ceilings in general, it sounds to me like substandard workmanship and stupidity! Good building practice requires that the roof is completed before ceilings are installed. You need to make sure that the ceiling is thoroughly dry and the builder must repair the holes he has poked in the ceiling board. If he is unable to do this to your satisfaction, you should probably demand that he replaces the ceilings. I don’t know what sort of a contract you have with the builder – or whether he is a member of the NHBRC. These two issues will make a difference.
I have a “Minor works Agreement Contract prepared by the Joint Building Contracts Commitee Inc” with the builder, and they are a member of the NHBRC. How will it make a difference? Thank you for your help!
Since they are members of the NHBRC you can call the NHBRC and ask for assistance in sorting out the problem. I assume they would check the contract as well. Perhaps you should read through the contract to see what protection it offers you as the client in a situation where damage is caused by the contractor.
Hi, I just bought a house and 6 months later climbed into the roof and saw that my now tiled roof still has the old Corrugated roof in place. my concern is that the distance between rafters are about 1200mm to 1400mm (approx) apart and still has the corrugated roof on it with the tiles placed ontop. Should I be concerned? I was informed that this House has been standing 15 years like this.
Brandon it depends on the type and weight of the tiles. Some time ago it was trendy to lay pressed steel tiles over metal sheeting; to get the look of tiles at a cheaper price. If they have been there for 15 years, I don’t think you have anything to worry about. I doubt that heavy clay tiles would have stayed up that long. But if you are concerned, it would be a good idea to get your roof checked out by a roofing expert. You might need to reinforce the rafters. On the other hand you don’t want to be conned into replacing the roof unnecessarily.
Hi Penny, the tiles are double roman tiles and not pressed steel tiles. I am thinking of getting a roof engineer in to asses the roof but have been worried about being conned into having to replace the roof. When you say reinforce the rafters would adding sister rafters onto the existing rafters add extra strength to the roof?
I would imagine so, but you’d need to get advice from an engineer. There is technical data here http://www.specifile.co.za/Ds/M/MARL002_OCT08_PDF.pdf?download=yes
from Marley on fixing their Double Roman tiles. It might be helpful in ascertaining the degree to which your rafters don’t comply.
Hi Wendy
We experienced a large hole in our lounge ceiling last Saturday after a severe rain storm (house 14 years old-never leaked before). We have insurance and have had a number of contractors out to review and report on the damage. The insurer sent a bloke who now says that the “valleys are incorrectly water-proofed – specifically that there is not enough plastic overlapping the joins. He says the specification is 100mm overlap. Taking this into account, he says that it is a latent defect and that insurance will not cover the repair of the roof only the ceiling. Please advise?
Is is this “bloke” in the pay of the insurance company? Makes me wonder. If your house has genuinely not leaked for 14 years – either you live in the desert and climate change has affected your region dramatically – or the roof has done its job for more than a decade; especially if you live in an area that has experienced some really bad rain in the past. I am not a legal fundi, but I really cannot imagine how a latent defect could rear its head 14 years down the line. I wouldn’t accept this response and would definitely take on the insurance company. Which one is it?
Hi Wendy
Thanks for the prompt response. I am of the same opinion-think they are taking a chance. The company is CIA. I am waiting for the response from the contractor who came in on Saturday and will take it from there.
Hi Penny
does this mean you cannot get a timber roof truss in South Africa with a span greater than 10m?
John the table that gives maximum truss spans for rafter and tie-beams (where 10 m is the maximum span) relates directly to the standard timber sizes that are commonly used, viz. 38 mm x 114 mm, 152 mm or 228 mm. But a manufacturer of roof trusses will engineer them to any specs, utilizing suitable sized members – 52 mm or even 76 mm if necessary – and laminated beams if need be. So the short answer is “no”!
Good day ,
please be so kind as to advise me .
My builders wants SABS V roof timber
when i go to hardwares like builders warehouse etc
they have
York timbers S 5
and
Saturn Toimbers S 5
is this the same as V 5 or not
will treully appreciate your advise
regards
Rajan
Jhb
SA
If you go to the York Timbers web site http://www.york.co.za/ops/timber.asp you will see a full list of the timber that they produce. The V timber (which is a visual grading) is all rough sawn, while the S5 (which is a good quality structural timber suitable for buildings and roofing) is planed, and will be more expensive. They have a sales office in Pretoria; you may be able to purchase directly from them.
Dear Penny. Flat Roofs are used in several countries for a patio or Star-Gazing Platform. Is it allowed in South Africa and under what conditions. Which regulation prevents it (if at all?)
Thank you for this interesting website.
Dirk
Dirk a “flat roof” is a misnomer because you need a slight slope to allow rainwater to drain. The absolute minimum is 3-5 degrees, though when it comes to patios and decks (which I presume is what you mean when you talk about a “star-gazing platform”) people often do construct semi-solid “roofs” with latte or similar materials that are laid flat. If you look at the new version of Owner Building in SA, there are some stunning pix that will illustrate what I mean. Our book, Patios and Decks also has some great illustrations, though sadly it is long out of print.
But to answer your question in relation to the regulations; Part L of the NBR specifies minimum roof slopes in relation to the type of roof covering used. Various types of corrugated sheeting may be used to achieve a minimum slope. Any other type of covering requires at least a 10 degree slope. I hope that helps.
Thank you for the prompt reply Penny.
However, the question is, if the double story house has a concrete slab as roof (known as a flat roof) or portion thereof, may one then utilise the roof as a deck / star gazing platform.
Where can one read if this is allowed. The building inspector states it will be regarded as a 3rd story which may not be allowed. I would like to know what the rules state in this regard and when it will be allowed.
Many thanks
Dirk
Sorry for the confusion Dirk. It sounded as if you wanted to construct a deck or patio with a flat roof 😉
The regulations talk about “nominally flat” concrete roofs, because they should have a fall of at least 1:50 for drainage, though the NHBRC manuals state that the minimum fall should be 1 in 80 (1 in 50 is good building practice to ensure that it isn’t any less than 1:80). That said, I can’t find anything in the NBR or NHBRC manuals that refers to use of a “flat” roof.
However I think it would be a safety issue. While “Public Safety” is covered in the building regulations, swimming pool fencing, and I am pretty sure also railings around raised decks, patios etc. fall under the local authority requirements.
There is an interesting discussion on this forum that discusses a very similar issue – even though it is in the UK. So in your case, I can understand why the building inspector states that it would be regarded as a third storey.
Funnily enough we are currently living in a house that has a “flat” roof over a section of the house. It is part of an extension that involved adding a second storey over a double garage. If you go to http://sans10400.co.za/extensions/ or click on this link, you will see what the extension looks like. You will also see how the patio, deck, platform (whatever you want to call it) has concrete balusters around the edges. There is a very slight run-off that doesn’t affect chairs, table etc.
Recently , our plumber while in the attic of our house, mentioned that there was no protective underlay membrane under the tiles.
We inquired from others in our complex and they all have underlay. Our house was the showhouse which we purchased from the developer 8 years ago.
We inquired why we did not have underlay and the developer said that regulations had changed between the time the showhouse was built and when the other houses were built. We need verification of this but do not know how to find out? Could you advise when the regulations changed. The house is less than a k, from the sea and my understanding from what I have so far researched is that all coastal houses should have protective underlay.
If this is the incorrect forum to pose the question could you kindly redirect me.
The National Building Regulations were first published in 1988 and then revised in 1990; and amended very slightly in 1993. The current regulations were published by the Department of Industry on May 2008 – and the deemed-to-satify codes of practice or South African National Standards (which are drawn up by the SABS), published progressively from that date. The last SANS were published last year. If you want to read more about this see an article I wrote for another website: National Building Regulations South Africa in 2010.
I have a copy of SABS 0400-1990 (renamed SANS 10400-1990) which you can download free from this site by clicking on the link above.
In Part L: Roofs, there is a general requirement that roofs must be “durable and waterproof”.
LL5 WATERPROOFING in the deemed-to-satisy rules state that, “For the purpose of runoff of water” any roof with specific coverings (and these include all types of tiles, fibre-dement, clay, metal, natural slate etc) must be constructed to a specific slope – which depends on the roof covering (for tiles it varies from 10 to 30 degrees depending on type). In all instances, the regs give an angle for a) WITH an approved underlay and b) WITHOUT an approved underlay.
For example, if single-lap concrete or clay interlocking tiles; concrete, clay plain tiles or shingles have been used, if there isn’t an approved underlay then the angle must be at least 26 degrees. If there is an underlay, the degree can be as little as 17 degrees.
Just as a matter of interest, in the 2008 legislation, the “durable and waterproof” clause changed to:
“is durable and does not allow the penetration of rainwater or any other surface water to its interior”… so it’s an expansion of durability and waterproofing.
So long story short; if your roof does not have a slope of at least 26 degrees, the builders broke the law! Sounds to me like they probably rushed the show house to start getting sales.
WOW – amazing how quickly & comprehensively you responded. Thank you.
Under http://www.thefacilitators.com/frequently asked questions I found this………..
Is it compulsory to put a plastic under the roof tiles?
Under tile membranes are a mandatory requirement in coastal areas and for tiled roofs having a pitch of between 17,5 degrees and 26 degrees or greater than 45 degrees. Under tile membranes are optional but recommended for roofs having a pitch of between 26 and 45 degrees. (Building Manual Part 3. Point 7.4.2)
It is the ‘coastal area’ part that interests me. Although we do not have any serious leaks in the roof, the downlighters only work intermittently, there is fine dust dropping where the cornices meet the wall/ceiling and recently in strong wind, big chunks of paint, fell off the bathroom ceiling! I am sure this is because of no protective membrane. I wonder if we have any recourse against the builders?
I tried to get into the site you mention, but it is for sale? In any case they are quoting the NHBRC Home Building Manual Part 3 – and what the manual says is not in keeping with the National Building Regulations. The NBR don’t differentiate between different areas; so for the NHBRC to say this is mandatory is nonsense. Even the deemed-to-satisfy rules set by SANS 10400 are “non-mandatory requirements, the compliance with which ensures compliance with a functional regulation” (which is a bit of a contradiction, I feel, since the requirements of the regulations state that they will only be deemed to be satisfied if the standards are adhered to).
And what they say is also not correct, bearing in mind that quote is the same as in the copy of the manual I have, which was published in 1999 – and therefore should be referring to what was then the national standard. Download the SANS and have a look at the table on Page 90 (Minimum angle of slope). My suggestion is that this is good building practice for coastal areas, and not mandatory.
As they say in the Introduction to the manuals:
“The Home Building Manual is based on normal construction procedures and recommended practices, which have been shown to be satisfactory and acceptable over time.” They expand considerably on the regs as such.
As I said previously, if the pitch of your roof is any less than 26 degrees (presuming the tiles are as I stated – viz. concrete, clay, or shingles) then I believe you most definitely have recourse against the builders. And the answer you were given by the developers is rubbish! That in itself should help your case.
Thank you. I have downloaded and will look through the SANS manual.
Just so you are clear: the first bit in each section REGULATIONS is the law (there is another free download on that same page which details how this part has changed – but I have included that info on the website) Below that is a section on DEEMED-TO-SATISF-RULES. This is the national standard which has been set by the SABS. This free document does NOT incorporate the changes made by the SABS between 2008 and 2011. Those documents are available through their website at a fee; or you can visit an SABS library to view them. The “manual” referred to is one of two produced by the NHBRC.
It occurs to me that whoever built your complex should have – by law – been registered with the NHBRC. If you know their name you can check on the NHBRC website. So you could, in fact, have recourse via this organization.
Apologies if I am sending this twice. I replied to your mail yesterday but perhaps I did not submit as I can’t see it on website.
Rabie Properties built our complex 8 years ago. They are thriving and active in our area and nationally, I think. They have not even acknowledged our letters, sent by email & registered post, asking for verification that the roofing regulations changed between the time of erecting the showhouse and the other units. We have the NHBRC Certificate so they were registered with this body. I shall try contacting them but I think they only cover roof leaks for a year and structure for 5 years. Do you think we should persue the legal course of action? With the new Consumer Protection Act we have to reveal that there is no underlay and thus the selling price would drop considerable or, in fact, the sale would fall through. Wish there was a way we could hold the builders responsible.
Dear Sirs/ madam,
I hope you can help…. I am constructing a house that requires custome raftes/ roof structure and I am looking for a engineer who can design them (Not make them – just design). Can you recommend some bodies?
I am sorry Chris, we don’t recommend people. Companies that manufacture roof trusses normal employ engineers to design them.
I have retired after 38 years in construction.What do i have to do to register, or become a competent person to supervise alteration and additions for the owner builder . I have noticed there is a gap in the market with the latest building regulations.
Albert a “competent person” is someone who is qualified and registered with the relevant organization. For example an architect, who must be registered with The South African Council for the Architectural Profession (SACAP). You can read more about the concept of competent persons here.
I am currently a student at CPUT, doing my Btech. I am thinking of doing my Thesis of the Behavior of Prfabrcated Timber Roof Trusses.
How do you determine the Behavior of Prefabricated Trusses and is there any test that need to be done.
Can you forward me any additional info which could assist me in this task.
Best Regards
Gerswin
You’re the one doing the thesis not me! I think the the FET Colleges Building Materials Level 4 covers this. But you’d best contact a reputable manufacturer of roof trusses.
A client has asked me to construct a patio roof around his house. there will two valleys that measure 7.2 and 7.5m in length. Do you have any advise as to how I can accomplish this with rafters?
Graham I am not a builder. I am a writer with a fairly good knowledge of the regulations – because of the books I have produced. It’s called research. If you have been asked to construct a roof of any sort, I would assume that you are a professional with training and experience in this field. If not, I suggest that you employ someone who is, or tell you client to go to a professional who can do the job correctly.
Hi there,
is there any regulation for building flat roofs??
Thanks
Brent
Part L of the National Building Regulations deals with roofs.
What provision must be made in the brickwork to anchor roof trusses securely before the superstrcture reach wall plate leve?
Danie it depends on the type of roof and the walls. This post on our sister site, OwnerBuilding, should help you.
This information is out of date. Timber grading system was changed about 10 yrs ago. Empirical designs should not be used as municipalities now require a rational design. Just go to The ITC web site and find a truss fabricator in your area.
Hi Angelo, When I originally put up this page, the relevant section of SANS 10400 had not been released. As you no doubt know, the sections were published progressively – over a very long period of years – and some time after the legislation was changed in 2008. As you also probably know, prior to this date, the then so-called “Code of Practice” for the NBR had last been updated in 1990. I was utilizing the information presented in the most recently published regulations.
I guess that you are referring to industry standards? Anyway, I have now updated the page and will be adding relevant tables today. Thank you for your interest and your comments. Please feel free to return whenever you are able to, and to make comments that will help others who visit our site. Thank you. Penny
Brandon I have updated the information about rafters. You might this useful.
I have added several tables that you might find useful.
I have added information about trusses that might help you.
John I have updated the tables for trusses, rafters etc. You might find this useful.
thanks Penny very helpful
Can you perhaps confirm the max building roof height of a double
storey building in a build-up area in Centurion.
Can I build another story on a double storey concrete slab roof into a
loft or is that not allowed?
To whom it may concern,
So far I have found your website very helpful but was wondering if you
could give me some more information or tell me who to contact with
regards to South Africa’s building requirements as they pertain to
roof access of a multistory building. I am a trustee at a complex in
Cape Town and our complex at its highest points is a six story high
building that has various sections to it, each built to different
heights which means that we have five different roof structures and I
wanted to know if the developers and or architects would have had to
have included ladders or other mechanisms to access each of the
various roof structures. Two of the roof structures are six story high
buildings and only the pitched roof has a ladder to access it and the
problematic flat roof has no access to it. We have had major problems
with regards to waterproofing and runoff on this flat roof and because
access to it is limited it has contributed to delays in repairing the
roof. The developer has said that no ladder appeared on the architects
drawings and as such wasn’t installed. Should a ladder have been
required to be put in by SA Building requirements?
Many thanks,
Samantha
Hi Samantha,
I am sorry to hear about all your major problems.
Unfortunately your proplems are specific to the type of hi-rise structures in more densly populated areas so a number of other factors will come into play. These could relate to town planning, local fire regulations and other by-laws that affect your building. I suggest that you contact the Planning Department in Cape Town at this number 0860 103 089 and speak to one of the building inspectors and explain your concerns.
i would like a quote on replacing two flat roofs
I am looking for more information regarding the specifications for the
installation of lightning conductors for thatched roofed houses and
lapas. Could you possibluy assis?
Our new house’s roof etc has not been properly completed and rain
comes into the main door,the contractor did not register us with the
Nhbrc for affordability, who do we turn to, we moved in on the 28 June
2012 and the contractor does not want to return to complete it as he
had a contract elsewhere.
Bev you have a problem. First of all registration with the NHBRC has nothing to do with affordability. The law states that all contractors building houses for other people MUST register with the NHBRC – and all houses must be enrolled with the NHBRC. Owner builders who are constructing their own homes may apply for an exemption. So basically the contractor has broken the law. You should report the builder to the NHBRC so that they can take the necessary action to prevent him from ripping other people off!
Hi Alan,
I am sorry but we are not contractors and we do not undertake any building work. Our aim on this website is to inform, and try to help the public understand the National Building Regulations and associated matters.
Hello, my husband and I are interested in buying a house. The owner recently “replaced” the roof, but there are no building plans, only sketches about the work that was to be done. When we enquired about a warranty for the work done, the builder said that he can’t give a guarantee on the materials used or the work. Is this normal? Also, it is a “flat” roof – which I undestand does not really exist, because all roofs needs to be lifted. The builder also claimed that he lifted the roof to 7 degrees. Is this enough?
Wow very interesting site… i am structural designer / Roof Designer in the Timber industry… using one of the best system’s software. This will be my favourite site from now on…
If there are no plans for the house, then the house is illegal. DO NOT BUY IT.
We recently updated our Roofing pages, have a look at these for more info on pitches and flat roofs.
Here are the links:
Roofs
Waterproofing of roofs
Could u please supply a drawing which shows a cross section through a thatch roof that sits on a load bearing 220mm wall.
Need to assist my gr12 learners with their PAT (Engineering Graphics Project)
thanks
We do not offer a drawing service and don’t have anyone who is competent to do them anyway. I suggest you go to your nearest SABS office and have a look at SANS 10407, Thatched roof construction. Chances are you will find a drawing here that will suit your needs. Since it is for learners, they will probably photostat the drawing for you. Good luck.
Hi Thinus,
The National Building Regulations is the law and they are followed and used in conjunction with the SANS 10400 minimum guidelines. Every local council does have it’s own local planning department and it will be up to them to say what you can and can’t do. A “competent person” (a qualified draftsperson, architect or structural engineer) in your area could also be consulted and they will be able to help you with this.
Hi
I’m renovating my house and try do keep it diy. I know – dangerous! I have a kitchen / dining room / lounce I want to convert into a single open plan area. The dimensions are appr. 11 x 7 meter. it used to be three rooms. The roof is tiled. Unfortunately the pitch of the roof spans over the 11 m side. It has a wall approx in the center, but only half way through the 7 m side. It does not look like a load bearing wall, but the roof sections are resting on a brandering on top of the wall. I can see a small height difference in the ceiling between the supported section and the unsupported side which is concerning. Could you refer me to someone for expert advice that does not cost an arm or a leg?
/ \————\ 7 m section \————\
/ \————\————\————\————\
/ \————\————\————\————\
/ \————\————\————\————\
/ \————\————\————\————\
/ \————\————\————\————\
/ \————\————\————\————\
/ \————\————\————\————\
|=================================== |………………………………………………………|
11 m section —->################
# <—————————————————-| Support wall
# +/- 4 m with 3 m
# unspported
Sorry for the lame drawing, but thats what it looks like.
Any advise will be appreciated.
Hi Johann,
We have put up a page with a few pointers for you on this page thatch-roofs-and-lightning Just click the link. I hope this helps.
In the event that a steel roof has been installed, and there appears to be issues (e.g. leaking), and the builder IS registered with the NHBRC, what would be the logical route to follow the resolve the issue (e.g. have roof repaired at builder’s cost)?
Johan, There is another SANS 10313 (2010): Protection against lightning – Physical damage to structures and life hazard, that you should refer to. In addition, all lightning protection systems (which include masts/conductors) must comply with the requirements of SANS 62305-3 and the earthing of LPS must be bonded to fixed electrical installation protective earthing in accordance with the requirements of SANS 10142-1. So it probably won’t surprise you that for safety reasons, both LPS designers and LPS installers must be competent in terms of the job. In fact SANS 10313 provides for the issue of anLPS installation safety report by and LPS designer or installer, as well as an LPS maintenance certificate.
There are several other “indispensable” SANS that SANS 10313 refers to as well, including those dealing with the wiring of premises and protection against lightning.
One of the biggest problems is that the presence of conductive materials can lead to sparking inside the thatch, which is a fire risk. So the Standard specifies where the metal is installed, how masts should be protected and earthed, what the clearance distance between the thatch and metal objects under thatch should be.
This is not a DIY job!
Hi Hein,
You have to follow the method set out by the NHBRC for any conflict resolution. The NHBRC should have done a waterproof inspection as well. The first thing they say you should do is contact the builder and give him the opportunity to rectify the problem; this should be done within 3 to 7 days. You should put this in writing and get a signature when it is delivered (preferably registered post). If you get no response then you can contact the NHBRC. If your building was registered correctly and the fees paid then the NHBRC will investigate and if the claim is valid they will undertake remedial work. Do not just go ahead and do the work without checking with the NHBRC first you might put yourself at risk of not get your money back. You can read more and download the complaint form on our Owner Building site >>Click Here<<
Hi there
Looking for some advice.
Busy building a new outbuilding and entertainment area. Simple structure (L-shaped layout). In terms of roofing, we have decided to go with corrugated sheeting to match our house. What is the minimum slope for a single pitched roof? The areas to be covered are: 10m long x 3.8m wide and 6m long x 4.6m wide.
Any advice would be greatly appreciated.
The recommended pitch + rafter sizes as specified in the building regulations are all shown in tables on this page. However a competent person should be drawing your plans for you and they will be able to specify specifically for the design required and materials to be used.
Thanks.
Yes, proper plans were drawn up and approved. Materials are also specified in the plans but for some odd reason the roof pitch isnt indicated so want to make sure what it should be instead of taking the builders’ word as to what it should be.
Thanks again.
Great site by the way.
HR
Looking at the specs we quote in Owner Building, 5 degrees is the minimum allowed for corrugate “iron” roof sheeting; but anything less than 15 degrees is regarded as a flat roof. The tables seen to indicate 26 as max. Just remember that according to the regs any pitch less than 26 deg and greater than 45 deg should have a damp-proof membrane (which is good building practice in any case). The degrees specified for corrugated fibre-cement are different. Why not ask the person who drew up the plans what pitch was intended?
Great, thanks for the advice. Really appreciate your help.
Will also confirm with the architect.
All the best.
HR
We moved from Nelspruit to Hazelpark in Germiston 2011 and purchased a house. Since we moved in (Jan 2011 – we complained to the agent about the roof leaking. The lounge ceiling was replaced by the previoius owners, insurance company. The contractors did not fix the actual problem – the roof tiles. The house was registered in May 2011. The same problem occured on the same place on the lounge ceiling as before. I paid contractors – to fix the tiles. Suprise, when it rained again – we had the same problem. I contacted them again and they came out and confirmed that they have fixed the problem. The third time it leaked again – and called the same contractors to come and inspect. Now it was fixed, but the ceiling is damaged very badly – it made buldges and big stains. The contractor said I must contact my insurance company and ask to repair the ceiling. The insurance company refused to repair as they said it was bad workmanship from the roof contractor. They also had a roofing specialist who confirmed that the roof was badly constructed.
The roof next to the lounge is so badly done – if you are outside the tiles is laid down uneven and the roof is very low. On the inside there is not a celing board but woodpannels. This started falling out and when it rains water runs down on the wall on the inside of the room. I think this was and stoep that the previous owner converted into another room.
Please advise what we can do.
Hi
Can someone assist with the regulation for a flatroof with sheet
The NBR regulations for roofs are pretty well spelled out on this page. What else do you want to know?
Sonja, Unfortunately most house sales in SA are voetstoets – which means that you basically get the house the way it is. If you were mislead in any way you will have a comeback – e.g. If there was a latent defect. This MIGHT be regarded as a latent defect.
I am not sure what you can do, though if this is a “contractor” that did the work, the business should be registered with the NHBRC. Further, if it was a business utilized by an insurance company, the insurance company should (would?) not have used anyone that wasn’t registered with the NHBRC. You need to go back to the original insurance company and see if they can help you force the contractors to rectify the problem. (It isn’t clear if the same contractor did all the work – on all occasions). If they did not fix the problem then they are probably liable for the damage to the ceiling. But if they are the same people the insurance company called in (or approved) initially, then the insurance company must surely have some liability in terms of sorting out the problem. I can’t be sure.
If this is due to a latent defect – the way you describe the roof it might be – then you may have recourse to the seller. But you will need to get legal advice on this.
Hi. I live on the top floor of an apartment building. Some time ago I
noticed serious cracks developing. I got an engineer out and he told
me that the concrete roof has no expansion joints, thus causing all
the other damage. The developer denies it is his responsibility to
fix. What are the legal requirements for a concrete roof to be
structurally sound?
If you click on the link at the end of this page (waterproofing of flat roofs) you can read more about drainage and waterproofing of flat roofs. Scroll down to the heading “Drainage and Waterproofing of Flat Roofs” … and “Flat Concrete Roofs”.
SANS 10400-L: 2011 only refers to expansion joints twice:
4.3.2 Gutters and downpipes
4.3.2.3 The position of all outlets shall be at least 500 mm away from upstands, parapet walls and 1 000 mm away from expansion joints.
4.3.3 Flat concrete roofs
“4.3.3.1 Unless the expansion joints are designed by a competent person (built environment) to accommodate the flow of water over such joints, twin kerb upstand-type joints (see figure 3) shall be installed over expansion joints in concrete roofs, which shall be located away from outlets.”
The implication is that where necessary expansion joints must be included in the design of a flat concrete roof.
To clarify this, one needs to look at the General Requirements:
“4 Requirements 4.1 General”
“b) flat roofs, in addition to complying with the general requirements of 4.2, are
1) in accordance with the requirements of 4.3, or
2) the subject of a rational design or rational assessment prepared by a competent person (built environment) and are inspected by such a person during installation,”
4.2 = Roof coverings and waterproofing systems
4.3 = Drainage and waterproofing of flat roofs
But it is not only SANS 10400 that must be adhered to, there are other SANS, primarily SANS 10100 Code of practice for the structural use of concrete Part 1: Design (itself a document comprised of more than 200 pages) & Part 2: Materials and execution of work.
Part 1 covers movement joints and the need for movement joints.
“Many factors influence the tendency of concrete to crack, and the limitation of such cracking is also influenced by many factors, probably the most important of which is the proper provision of adequate reinforcement. However, there are cases where the most appropriate or indeed the only control measure is a movement joint.”
“In common with all other structural materials, concrete expands when heated and contracts when cooled; it also expands when wetted and shrinks when dried. It also undergoes other strains owing to the hydration of the cement and other properties of the material itself and of its constituent parts. If these expansions and contractions are restrained, stresses will occur that can be of sufficient magnitude to cause immediate cracking of the concrete, or cracking will occur later owing to fatigue failure resulting from long-term repetition of the stresses.”
Of course there is a lot more information in the Standard, which also looks at different types of movement joints including contraction joints (a deliberate discontinuity but no initial gap between the concrete on both sides of the joint); expansion joints (a joint with complete discontinuity in both reinforcement and concrete and intended to accommodate either expansion or contraction of the structure); sliding joints; hinged joints; and settlement joints.
In the section on Provision of joints, the Standard states that joints can minimize the “risk of cracking due to thermal movement and shrinkage”.
I don’t see anything that relates specifically to roofs.
At the end of the day it was the developer’s responsibility to build correctly and if expansion joints were not included, then it is his responsibility to fix the problem.
All structures must be safe and sound … simple. And anyone with even the basic knowledge of concrete technology will know how important expansion joints are.
According to the definitive Fulton’s Concrete Technology, Construction joints are provided in structures either to provide a convenient stopping point during construction, or to allow relative movement between various parts of the structure.
“They are a major cost factor during construction and, if poorly designed. detailed or constructed, may affect the strength, serviceability and durability of the structure.”
Hi. I recently moved into a unit in a newly developed block of flats in Jabulani Soweto. I live on the top floor of a 3 story building. I recently had neighbors move into the unit directly below me. I’m costantly disturbed by noises from their unit. I can hear their movements. I can hear doors opening & shutting, furniture movements and when they use the bathroom. Is this normal? I would like to know what the regulations & standards have to say regarding the thickness and soundproofing of roofs/floors for block of flats.
Please advise
Pearl, the National Building Regulations are material specific when it comes to floors and roofs – and walls for that matter. Since you are on the top floor, the roof is not relevant – but rather the ceilings beneath you. Is the building built with bricks-and-mortar (or blocks and mortar) – plastered – and is the floor concrete?
It sounds like a sub-standard building to me! You shouldn’t have the degree of noise that you describe.
I have done a search for “soundproofing” in SANS 10400 Parts J (floors), K (walls), and L (roofs) and the word is not used in any of these sections of the NBR! Insulation for fire protection is more important. But if a concrete floor (for instance) is built according the relevant SANS, it should be sufficiently thick and insulated to block out sound.
Unfortunately we can’t do referrals. Any reputable roofing company should be able to help. Get quotations from a few to compare costs.
Hello
What are the regulations regarding insulation for a flat roof.on a granny flat.
Thanking you
Cheri the regulations for insulating and waterproofing a granny flat roof are exactly the same as for any other “flat” roof.
Insulation is mentioned in the National Building Regulations, but there is not a lot of information available. There are several other Standards that are available from the SABS that apply. However these are Standards for the insulation itself – and its installation.
SANS 10400: X & XA (Environmental sustainability & Energy usage in buildings) only mentions insulation in relation to metal roof sheeting.
SANS 204: 2011 Energy efficiency in buildings has a comprehensive section on roof assemblies that deals with heat flow etc. It has information about emissivity and reflective foil insulation used for “flat” roofs and other insulation materials. This relates primarily to the R-value [“measurement of the thermal resistance of a material which is the effectiveness of the material to resist the flow of heat, i.e. the thermal resistance (m2·K/W) of a component calculated by dividing its thickness by its thermal conductivity”] as well as the climatic zone in which you live.
All roof assemblies (including your granny flat roof) have to achieve the minimum total R-value that is specified in a table that five the direction of heat flow. For example, I live near Cape Town which falls into Zone 4 and roofs in this zone “are required to achieve a minimum total R-value of 3,7 in the upwards direction (see table 8). A pitched tiled roof with a flat ceiling in climatic zone 4 achieves a total R-value of 0,35. This means that additional insulation that achieves a minimum R-value of 3,35 (3,7 to 0,35) in the upward direction is required to be installed in the roof. This can be achieved by installing bulk insulation or a combination of bulk and reflective insulation.”
Then there are regulations that relate to how the insulation is installed and supported…
I think you’d do best to contact a company that specializes in insulation products for roofs.
Hi, our roof is not repairable and has to be replaced. We are thinking
about changing from flat roof to Apex. Do we need permission, have to
check with neighbours, plans etc. Please advise.
Regards,
Haidi
Haidi, you will need to submit plans to your local authority, and the roof must be built in accordance with SANS 10400: Part L Roofs, which is covered in some detail on this page. The only time you have to ask for neighbours’ approval is when you need special permission to do something e.g. if you are not complying with the NBR. The most common issue is when people want to build on or close to a common boundary (though in Cape Town now, with the new zoning regulations, neighbour’s consent is no longer required).
hi penny
Do powerfloated parking decks that are drained need to be waterproofed in term of the nbri or san 10400
Many thanks
Hi Prak,
Apologies for taking a few days to reply, but I must admit I was a little taken aback being asked a question by the CEO of a respected firm of architects. 🙂 We appreciate it and take it as a complement.
Having said that let me try and answer as best as I can.
As you know the intention of the regulations is to ensure that all buildings are to be waterproofed according to their designated use. It sounds as is if the floor that has been powerfloated is not on ground level (a parking deck) but does it act as a “roof covering” for a ground floor area that is not for parking? I think that the drainage on a parking deck would be mandatory and if it is a “roof” for an area other than parking then waterproofing is essential.
Two other comments:
1. The NBR and SANS 10400 is not intended to be a building handbook. The Introduction to Part A states: “The National Building Regulations do not purport, and were never intended, to be a handbook on good building practice. They set out, in the simplest and shortest way possible, requirements to ensure that buildings will be designed and built in such a way that persons can live and work in a healthy and safe environment.”
In addition “fact that a building complies with the National Building Regulations does not necessarily indicate that it is a desirable building”.
“In the case where the designer of a building is not professionally qualified, there is a wealth of information on good building practice available in textbooks and from organizations such as the CSIR, the South African Bureau of Standards, the National Home Builders Registration Council, the South African Institution of Civil Engineering and various trade associations.”
ie The regs (SANS 10400) state very clearly that not all elements or procedures are detailed in the regs.
Apart from other textbooks, a qualified concrete technologist would be able to advise whether additional waterproofing would be needed. eg There are a various admixtures that can be used to improve dampproofing.
2. I don’t believe powerfloating is even a factor here. More important is the concrete mix design and any reinforcing (including its placement) required.
Hi,
I bought my house(Kempton Park) about 4 years ago. I have had some alterations done and addad a double garage. Now I want to knock out a weight carrying wall inside my house. living room was extended by the previous owner, now there is a split in the middle. I was told a laminated beam across could carry the roof load. the span of this wall is 3.5 meters. How do I go about this job.
I had an engineer come out 2 years ago, still waiting on a quote. Tiled roof 26.5 deg pitch built with King post trusses.
Marius if you can’t find the engineer you asked for the quote, I think you should probably find another one. We really can’t even begin to try and give you this type of advice. You need professionals on the ground who can visit your house and make sure it is all going to be done properly.
Hi Penny, thank you for the advise regarding expansion joints for flat roofs. I was just wondering, with the new building regulations that came into place in 2008, how does that affect the regulation/standards of roofs constructed before the amendment was passed in 2008.
They don’t affect old structures unless there are major renovations that require plans. (as I understand it)
Can you please provide me with the correct slope on a corrugated roof of a carport with a width of seven meter. The carport is open on the sides.
Hi Kerneels,
The regulations for corrugated pitch roofs say:
4.2.2.1 Roofs shall be provided with a pitch of not less than that given in tables 1 and 2, provided that sheeted roofs without hips and valleys in category 1 buildings may have a roof slope of 5° subject to all end laps in such sheeting being sealed and having a minimum lap of 250 mm. The slope of valleys in such roofs shall not be less than 11°.
Table 1: Corrugated (including box rib) profile (galvanized iron, polycarbonate and fibre glass) 11 to 22 degrees.
You can read more on this page.
What type of roof anchors is required when doing maintenance on asbestos roofs. Is crawl boards necessay
First of all Irvin, If the roof is indeed asbestos, then you need to take special precautions when working with it. I will put up a new post on asbestos in the next few days and send you a link. Hopefully it is fibrecement.
Use roof anchors recommended for the type of roof sheeting used – most building and/or hardware suppliers will advise. The actual size will depend on the structure of the roof – timber members in particular. It is advisable to use a crawl board.
what is the normal grade of timber used to span 20+m the truss designers have used a fink truss design. the roof carries concrete roof tiles and the pitch is about 26 deg. they have used grade 7 SAP
Are there any building regulations related to irrecting objects on roof tops e.g Solar panels/solar geysers that should be followed to avoid citations or can a person proceed without fear of intevention from concerned agencies.
The building regulations do not cover erection of solar panels and solar geysers on roofs. The local authority may have by-laws that affect them.
Hi Barrie,
The truss designer is obliged to give a certificate that states that the truss was manufactured in accordance with SANS 2001-CT2:2009 “Structural timber work (roofing)” This SANS though does not specify timber classes. The Agrément certificate for the approved system used by your manufacturer will have those details. You can ask who the manufacturer was and find out if the softwood timber (SAP) that was specified meets the specifications. You may also get the details from the Agrément SA website. We mainly deal with the SANS10400 on this site but help where we can. There is a technical article by Professors W M G Burdzik & N W Dekker that might interest you here: Burdzik_Rational(2012)
Hi,
I would like to know if I need building plans drawn up and approved for a lapa (with a concrete tiled roof) less than 20 square metres in size?
Nadine, if it has a tiled roof, you need a properly built roof structure and so it is quite likely that your local authority will need plans. You need to ask them – ultimately they have the last word.
i have a two story plan which is 410 m2 on the ground floor, and 120 m2 on the top floor, the projet will be on the farm, is it possible to use maxi brick and if yes, what should be the strength of the composition
Hi James,
Yes it is possible to use maxi bricks for your project. If you are in South Africa then BY LAW you will need to submit plans done by a “competent person” for example an architect. Bricks in SA need to be made to strict SABS specifications the same as any brick manufacturer does. The other organization to approach is the Cement & Concrete Institute at this link: cnci.org.za. It does not make any difference if you are building on a farm if you do not submit your plans for approval before you build then you will be breaking the law.
Morning,
We are building a log home and I have heard that it is not a good idea to plant the “thatching” poles in cement as cement can “attack” the poles. Is this true?
Timber poles are less likely to rot if buried in concrete rather than in the ground, but you should always use some sort of sealant on the ends first – e.g. bitumen. The concrete forms a foundation footing which will be required if the house is “a pole structure”. BTW cement is a powder that is used with sand, stone and water to make concrete; it is never used on its own.
Hi there,
I’m trying to find out what is the minimum roof angle, I have recently been told that the law for roof angles is 21 degrees.
The complex that i stay in was built in 1950 with a roof angle of 18 degrees.
Which has concrete tiles.
Please could you let me know what the correct degree the roof should be at.
Regards
Cora
Hi Cora,
I have put your query on our “Roofs” page here: roofs As you will see on the tables that for concrete roof tiles with an underlay the pitch is 17º and without underlay is 26º. But the regulations recommend checking with the manufacturer.
how do u calculate the the minimum height of the king post in relation to the length of the hall for the concrete roof tiles?
Bethuel let me know the answer and what score you get for your assignment. Good luck. BTW “hall” for concrete roof tiles? Not sure what you are doing here.
Hi I would like to know whether thatched roofs enquire gutters for the release of rain water or how does it release the rain water?
Good day
Could you kindly assist with what height a flat concrete roof is built to, above level ground. I am doing a college project on solar panel installation in a rural environment and urgently require this dimension for my water pressure drop calcs.Many thanks for any assistance.
Kind regards
Mark
Mark, to be able to give you this information and ensure it is accurate we would have to do some research. Since it’s for a project, please do the research yourself. Contact people who do solar panel installations. Good luck.
Mkholisi, The water flows off the thatch, but there should be a skirt of concrete or paving around the foundations to help channel the water away from the house. This is why thatch roofs require a steeper pitch. The thickness of the thatch is also specified in the building regulations. You can read more in this article about waterproofing roofs.
I have had a duratile roof fitted by Roofix 66. They are extremely unprofessional and untidy. There are exposed nails all over, and when I asked them about it I was told that is normal with these tiles. That can’t be right, surely?
No Nadine it isn’t normal at all. Here is a link to the way that they should be laid. Your best bet is probably to get a representative from Duratile to visit your site and give an opinion. It looks as if they have offices in Durban 031-9404484 and Brakpan 011-7401549. If you live elsewhere they may be able to send a reputable installer to check for you.
BTW I did a Google search for Roofix 66 and came up with nothing! It is also best to use reputable companies to avoid this type of problem.
Hi,
I am designing a low cost building. They asked for a wooden roof (no roof tiles, no steel sheeting) what does the building regulations say with regards to this?
First of all Monique, with all due respect, you should not be designing anything if you are not au fait with the National Building Regulations. Legally you need to be a competent person to be allowed to draw and submit plans!
Even reading what I have posted on this page – which quotes the National Building Regulations and Standards Act – you should be able to tell that a roof has to be constructed in such a way that it will not be adversely affected by weather conditions – including the penetration of rain water. You have to have some type of SABS-approved covering.
Hi
i just want to know, what is the maximun roof span for flat roof.
Penny
I am building a house for somebody, but insists on a roof with a ceiling right at the top.
So, no normal trusses. Laminated pine beams, will do the trick,I think. However I need some formulas
to calculate the stresses,the right spacings and thicknesses of the beams.
Unfortunately the total length is 10800 x 6200. That involves the open plan kitchen and lounge.
Martyn I am not qualified to give you formulae. Apart from which the rational design of the roof needs to be done by a person who is competent and qualified to do so, and it needs to be approved by the local authority. If you are not competent to do this, you will need to employ someone who is.
You’ll need a structural engineer to design and certify the roof.This is a mandatory requirement in terms of the National Building Regs.
Hi to all
I have a problem, I had a storm that damaged my tiled roof, The house has been built over 20 years and has always brushed off the forces of the winds. Now my insurer says that they not covering my house as the roof was DEFECTIVE WORKMANSHIP. Meaning that the purlins are to far spaced apart to far. I know the law now states 760mm for tiles, but what was the law 20 years ago.
Kind regards Jose
Penny,
I am building my own house out of my pocket. The roof is flat with laminated beams, any suppliers who might quote me for a good product at reasonable prices
Is it very uncommon to use a 38×114 SAP as purlins for a metal sheet roofing. My spacings of Rafters are 1.2m
Penny,
We bought a house about 4 years ago that was built 40 years ago and has a flat metal roof.
We had a hailstorm and the roof leaked a lot. The insurance company sent someone to check and according to them the roof is not built according to standard and therefore they are not paying any damages (it has a pitch of less than 5 deg). They also said that in future they will not pay until the roof is fixed,
What can I do and whom can I contact?
Regards
Hi penny,
i’m a competent person and busy with alterations and additions to an existing house. the client has decided that the old asbestos roofsheeting and very old roof structure needs to go aswell and he wants a new hipped roof over the existing house and a new double garage at the front. the house has been renovated a couple of time before so you can imagine the roof condition from having different types and slopes of roofs everywhere! that’s why he want a totally new roof which look modern etc.
the problem is, the width of the house is about 10,04m measured from internal wall to internal wall. i went through the building regs and they say the max. span for timber trusses is 8m.
We have an engineer anyways to sign-off the roof but will it cover this “special” wide truss?
regards
As a competent person Brynn I would have thought your knowledge of the regulations would be much more thorough than mine. I assume that your engineer would need to draw a custom plan for the roof that accommodates the measurements safely.
Thomas, several thoughts. Firstly, the National Building Regulations and Building Standards Act was only promulgated 36 years ago (1977) and there is no law that states old houses have to be redesigned or rebuilt to meet the current regulations.
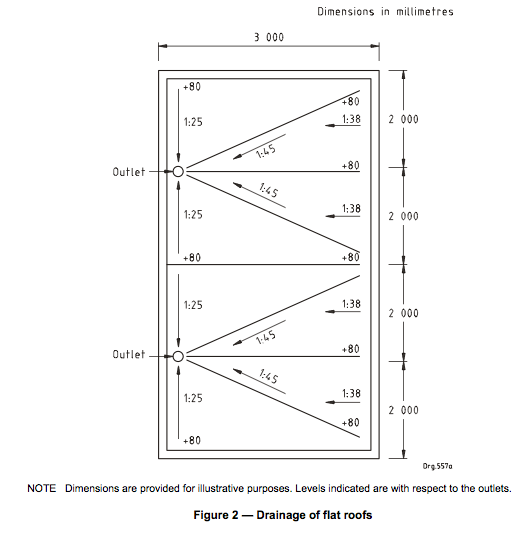
Secondly, you need to check your insurance policy carefully to see whether they state anything like for e.g. the house must be built according to current NBR or whether damage caused by “an act of God” (which is what a hailstorm is) would be covered.
Thirdly check the fall of the roof according to the current regulations, viz:
4.3 Drainage and waterproofing of flat roofs
4.3.1 General
4.3.1.1 Flat roofs shall have a fall towards external gutters, outlets or roof edges of not less than 1:80 where there is no interruption in the flow of water, and 1:50 where there is an interruption in the flow. Where two directional falls intersect, the minimum finished fall of 1:80 shall be maintained along the mitre. (See figure 2.)
Jacobus, the purlins required for sheeting should be considerably more substantial than the battens used for tiles. Have a look at the dimensions specified in the table above – Maximum Clear Spans for SA Pine Purline Rafters or Purlin Beams Supporting Profiled Metal or Fibre-Cement Sheeting Pitch – 26 deg. Working backwards, with a 1,2 m spacing, you should be using either 50 x 152 mm, 50 x 228 mm, or 76 x 228 mm purlins.
Patie, Unfortunately we are not in a position to recommend suppliers.
Hi,
I need some advice please. I’m extending my tile roof with 2.2m to cover a patio. The length of the patio is 3.3m. What is the minimum size of the supporting beam? The beam will be supported by brick pillars on each end and the roof pitch 11 degrees.
Thank you.
Jose, the previous regulations published as SABS 0400-1990 are available for free download HERE. They have included many more specifications in the new regs.
Pieter you need approved plans drawn by a competent person to be able to do this legally. That person will advise regarding timber and dimensions.
HI can anyone help me or give advice?
I bought a house in an estate, which had an existing carport( only paved and covered by a louver roof)
now there seems to be problems brewing about these roofs and apparently they want us to remove them. Is this legal? Do we need any plans for these roofs?
Subject:
Roof Question
Message:
Hi, I have bought a house 14 months ago. There is no isolation in the
roof. It has 2 sections of a Gable roof type with a flat roof between.
Tile roof type. Is this within the minumim requirements of the
building code. If not where can I get an inspector that can help me
get this fixed by the contractor/developer.
Regards.
Willem
Willem there is fairly detailed information from the Building Regulations on this page, however if it is not sufficient, you can either buy your own copy of this part of SANS 10400 (i.e. Part L, Roofs), or you can go to an SABS library where you will be able to read the Standard. You will need to approach your local authority if you want a building inspector to take a look at the roof, or alternatively get an independent roofing specialist in.
Hi Penny
I am designing a single bedroom, lounge, kitchen, timber dwelling and was wondering on the following?:
a) What would the floor loading be, as it is a suspended timber floor.
b) Where would I get the fibre stress figures for my calculations (SANS regs too expensive to buy) regarding timber grade 5,7 & 10.
Hi Balerit, Any one of the better timber merchants and or roof truss manufacturers will have those specs to hand. MiTek truss manufacturers are national and you can find their contact numbers here: mii.com/site/
Hi Stephen, There is no set standard amongst the municipal councils in SA when it comes to this situation, some want plans others not. The best I can suggest is you contact your local council planning department and find out what their rules are.
Hello, kindly advise me what the maximum height of a parapet is to be when using standard clay bricks and M140 concrete blocks ? i have searched in the regulations seen not to be winning. thank you
Hi Taku, SANS 10400 Part K-Walls has this in paragraph 4.2.5.1 “Balustrade and parapet walls shall not be less than 1,0 m in height”
and
4.2.5.2 Free-standing balustrade and parapet walls shall have a thickness of not less than the height of the wall above the base divided by
a) Solid units:
1) no DPC at base: 5,0 2) DPC at base: 4,5
b) Hollow units that have cores filled with infill concrete: 1) no DPC at base: 4,0
2) DPC at base: 4,0
Hi Habat, The span can be as wide as the size of the beams will allow, but the wider you go the bigger the beam will be, the pitch of the roof will also need to be considered. A Structural Engineer or Architect will be able to advise you on your specific needs.
Willem,flat roofs……brandering strips equi-spaced.Grading’falls must be indicated’n specified,expansion joints,roof covering’n finish specified.The authority in the municipality of your town can present you the SABS 0143 for authenticity
Subject:
Information regarding timber grading
Message:
Hi I would like to find out what it means when you are building with Grade 5 SA Pine, were doing an extention on our house with timber, it says they will use grade 5 sa pine timber, how do I know if they are using the correct timber. We have also had a lot of rain and our skeleton timber and roof trusses are wet, how long should one wait before you can start cladding the wood, and is grade 5 pine treated
for getting wet.
Thanks
Adele
Whats the difference between fibre glass and rubber flat roofs?
Jack we don’t get rubber roofs as such in South Africa. I think you a referring to a UK product. Fibreglass is generally used for sheeting and is normally corrugated. Sorry I can’t be more helpful.
Adele, all structural timber is graded according to specific SABS specifications. Grade 5 is for compression parallel to the grain of the wood. The grade mark is displayed on the timber which is usually CCA treated. The timber has no protection from water – which is why it should be covered on site.
The problem with getting water on roof trusses is that they can warp. They should dry out without too much of a problem, even if still damp when the tiles or sheeting are put on.
Is it compulsory to have the plastic sheeting under the roof tiles for waterproofing?
I have recently just bought a place and the geyser pipe burst and on inspection I noticed that there was no waterproofing or plastic sheeting under the roof tiles?
Sandro, it is compulsory in certain circumstances, specifically, as per Part L of SANS 10400, Roofs:
“4.2.2.6 Undertile membranes shall be laid loose so that water can drain between rafters and shall be installed strictly in accordance with the manufacturer’s instructions where tiles, slates and shingles are laid
a) in roofs that have a pitch of less than 26°, or
b) in roofs that have a pitch of 45° or steeper, and
c) in those areas between the coastline and an imaginary line 30 km inland, parallel with the coastline, or the top of the escarpment or watershed of the first mountain range inland, if these are less than 30 km from the coastline.
NOTE The entire area of jurisdiction of any local authority, the area of which is cut by the line demarcating these coastal areas, is taken as falling within the coastal area.”
Hi,
I have a new tiled roof (+- 4yrs old)
We noticed that the walls started building up Damp
Inspected the roof tiles and one tile had a small crack in it (I then replaced)
We had a BIG rain storm again, winds were blowing VERY strong…
I inspected the roof tiles again and ALL were ok.
I then inspected the last row of tiles, lifted them up and saw that the plastic sheeting below the tiles
stops before the bricks, the plastic was also rolled up, looked like they were pushed back… With the
last heavy rain theses areas with the rolled up plastic were filled with water and from the looks of it
is running then down the wall between the brickworks. I have been told that the plastic is there to
keep dust out and against heavy winds, but surely it must assist in times like my problem as well?
My questions:
1). The plastic underneath the tiles/brandings, should this not be pulled over the edge of your wall
plaster work?
2). Is this something that I can call the Builder or the Roof contractor back for to come and fix?
3). Please assist me with a solution to my problem.
Regards
Andries
Hello, i would like to ask what the appropriate size for timber wall plate is when using a currogated chromadek roof sheet on a pitched roof
I just wanted to find out where one could train to Grade Structural Timber (possibly a qualification of some sort). Would appreciate any help.
Jason I’m sorry but I have absolutely no idea. I suggest you contact timber suppliers and ask if they know.
Bukhali, All the specified timber sizes from the NBR are on this page. If it is not clear from this then I suggest you contact a Chromadek supplier and ask them. Alternatively contact Chromatek directly – they are based in Gauteng.
Andries this looks like the same question asked a different way? The DPC though is there as a barrier for DAMP – which includes rain – that is why it is called a damp proof course. As our page on waterproofing roofs states, “All roofs with a pitch less than 26 degrees or more than 45 degrees, and all roofs in coastal areas (to a distance of 30 km from the sea) should have an undertile membrane that is loose-laid so that water can drain between the rafters. If an undertile membrane is properly laid it will provide a very effective, impermeable barrier against wind-driven rain and dust. For this reason this particular SANS states that underlays should be provided for all slate and tiled roofs, no matter what the pitch (or slope), and where ceilings are not installed.” If it was not done according to the NBR which ultimately says – The National Building Regulations and Building Standards Act states that roofs must be designed and constructed safely so that they are not damaged by wind or any other natural force. The law also states that they must be waterproof (read the rest on the page I have linked to) … then the roof does not comply with the NBR which gives you every reason to call the boiler/roof contractor back to sort out the problem.
Hi
I want to span a timber fascia for 7.2m between 2 brick columns. The fascia is not a loading bearing member, and will only carry the gutter to collect water from an existing 7.2m wide fibre glass awning cantilevered 1.5m from a wall. Can I use a 228×76 Gr5 timber member?
Thank you
Hi Penny,
I have approved plans for the house with a normal gable roof with trusses. Now that I want to start building, I a m changing my mind about the whole. I want to build the house now and then later may be after 3 years get plans drawn to extend it higher into a double story house. So I am gonna reinforce the foundations with steel and the will use M200 blocks for outside walls and M150 for partitions and will get the engineer to check every thing. But my main concern is the roof if I put the concrete slab on top instead of roof with timber trusses will I be allowed by the municipal inspector or I must get new plans approved. In short I want a single story house now built with concrete slab as roof, m200 and m150 blocks and reinforced foundation with steel. Will this be possible. Thanks
Dumsani, The foundations are vital, so I would advise you get the engineer to specify the size and design and draw an amended plan of these. You will in any case need new plans if you are going to put a slab on top. There are very specific requirements in the NBR that relate to concrete roofs – which is what this will be.
Hi Gasant, The problem is the 7.2m span. You do not mention if there are any crossmembers to attach the facia to in-between the pillars. Over that length any thickness will warp and bend in time if it is not given any support.
Hi we are wanting to add a studio room to our house, currently we have a tiled roof. Do we have to use tiles on the extension room or can we use IBR/Corrugated Iron?
Yolande you don’t have to use tiles, but generally it looks a lot better if the same material is used. Either way you will need approved plans before you build.
Dear All
Is under tile membrane a Building Regulation requirement on a tiled roof ?
Please advise
Kind regards
Dennisthis is what the National Building Regulations state:
“4.2.2.6 Undertile membranes shall be laid loose so that water can drain between rafters and shall be installed strictly in accordance with the manufacturer’s instructions where tiles, slates and shingles are laid
a) in roofs that have a pitch of less than 26°, or
b) in roofs that have a pitch of 45° or steeper, and
c) in those areas between the coastline and an imaginary line 30 km inland, parallel with the coastline, or the top of the escarpment or watershed of the first mountain range inland, if these are less than 30 km from the coastline.”
Subject:
Battern spacing
Message:
What do the regulations state for the installation of 6.4mm Rhino board ceiling for batten spacing
Hi Trevor, Here are the reccomended specs from Rhino Board:
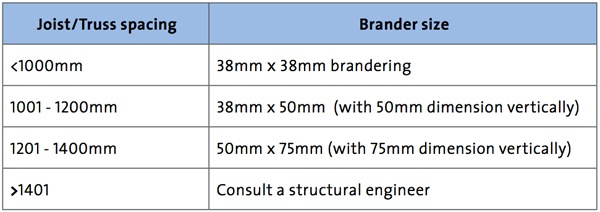
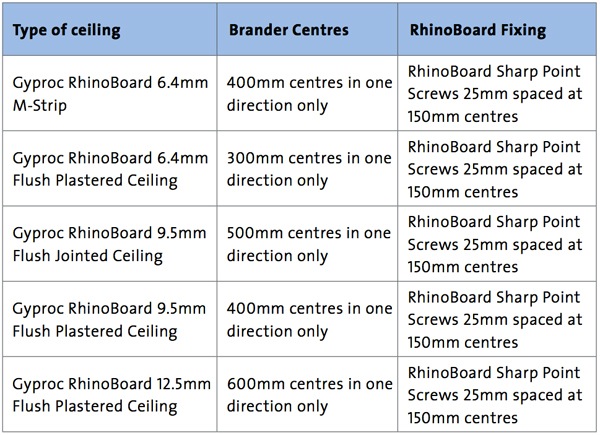
Fixing points for suspending the metal grid are required at 1200mm centres. Suitable fixing devices should be used when fixing to the structure, as recommended by fixings’ manufacturers.
Timber brandering can be fixed directly onto the joists/ trusses. The size of timber brandering used will depend on the joists/truss spacing.
Hi Penny,
I just bought a house and I found that the tiled roof does not have the under tile membrane. I took this matter up with the agent that sold me the property and this is their response:
“We do agree that there are new building regulations in place concerning the under lay ( plastic) of a roof.
The inspector, however, stated that the regulations apply to newly built houses. The act does not apply to properties older than 10,20 years and older.
The plastic serves as dust prevention, and not to keep the roof from leaking.
Tiles are the main factor that must prevent leakage.
The lifespan of the plastic under lay is about 15 years before it perish. Then you would have the same amount of dust on the ceiling, than not having the plastic at all.”
Is the above statement true?
Can i get advice on timber truss loading?
I want to estimate the loading for my eave beam design.
Lisa we really are not equipped to tackle this type of advice. I suggest you contact a truss manufacturer or a structural engineer. Apart from anything else, if you are designing roof structures you should be a professional – it must be done by a competent person.
Thank you Penny
The newest amendments to the National Building Regulations were in 2008, so in fact the age of the buildings referred to is not correct. what this states is:
“The roof of any building shall be so designed and constructed that it –
safely sustains any actions which can reasonably be expected to occur and in such a manner that any local damage (including cracking) or deformation do not compromise its functioning;
is adequately anchored against wind uplift;
is durable and does not allow the penetration of rainwater or any other surface water
to its interior;
does not allow the accumulation of any water upon its surface; and
as part of a roof and ceiling assembly, provides adequate height in any room immediately below such assembly.”
The deemed to satisfy SANS (specifically Part L of SANS 10400, Roofs) was only published in 2011.
This describes the roof underlay as the:
“flexible membrane fitted between the roof support structure and the battens”
It also states that:
“An undertile membrane, when properly laid, will provide a highly effective impermeable barrier against the ingress of wind-driven rain and dust. Underlays should therefore be provided on all tiled and slated roofs, irrespective of the slope and also if ceilings are not installed, so as to minimize the effect of wind-blown dust entering through the tiles.” So it is not just dust that they are concerned about. Going back to the legislation (i.e. the Act) the has been in effect since 2008, the roof must be designed so that it “is durable and does not allow the penetration of rainwater or any other surface water to its interior” And the new regs clearly state that the way to do this is to use an underlay.
The regs also state:
“Undertile membranes shall be laid loose so that water can drain between rafters and shall be installed strictly in accordance with the manufacturer’s instructions where tiles, slates and shingles are laid
a) in roofs that have a pitch of less than 26°, or
b) in roofs that have a pitch of 45° or steeper, and
c) in those areas between the coastline and an imaginary line 30 km inland, parallel with the coastline, or the top of the escarpment or watershed of the first mountain range inland, if these are less than 30 km from the coastline.” Clearly this relates to water and not just to dust! So that claim is absolute nonsense.
The key will be whether your house was built prior to 2008 or after 2008.
Can the plastic roof sheeting be installed without removing roof tiles? In an old home where the plastic has completely deteriorated, I have been told that the plastic can be installed from the inside using a staple gun. Apparantly this works and saves having to remove all the roof tiles and battens. Please advise.
Good morning,
I do not know if I can ask advice wrt the fitment of a Louvre deck? I live in a security estate, I want to have a Louvre deck build on the second floor of my home. The Louvre will be fitted by Suntek and will comply to the rules of the estate wrt colour scheme.
Do I need building plans?
Thank you.James
I’m not sure what you mean James – are you talking about building a deck or just the louvre over the deck. If you are building a deck you will need plans and probably also approval from the estate. You will also need approval from the estate for a louvred roof, but probably not plans.
Hi Penny,
Sorry for the confusion, it will be a louvred roof on my top floor. Basically I want to cover my patio with mentioned roof.
Thank you for the reply.
James you probably won’t need plans, but if I was you I would give the council a call and ask, in principle, whether they would want a plan – just to be sure.
Moki, since the plastic is fixed between the battens and the trusses, you should be able to install the plastic using a staple gun.
Good day
I am looking for the specifications of tying down the roof trusses to a brick wall, I have seen some specs somewhere here but it did not answer my question regarding the depth of wire inside the brickwork, The walls are build with maxi brick and I want to know what the depth of wire inside the wall have to be especially over the garage door openings as the specifications I saw did not sound right because the height of brickwork above the door was not enough to allow for this wire insertion.
Would appreciate expert advise.
Regards
C
I would like to make use of the “attic truss” shape, but it is not clear on what the max span would be and what the member sizes for that span needed would be. would you be able to help? Would my local council still “force” me to get an engineer to sign off on the “roof design” if I stay within these perimeters as given in this article?
Regards.
when the finishing is going to be a galvanised mild steel corrugated metal sheeting, how do you go about spacing the purlins and what are the proper steps to follow after the underlay has been fixed
William the specs for purlins for metal roofs are given on this very page. The building regulations do not specify step-by-step instructions in terms of fitting underlay.
They might do Stephan – it’s their prerogative. Unfortunately we are not qualified to do roof designs so cannot help you. BTW the parameters/specifications given here are from the National Building Regulations, so you must, in any case, be sure to stick to them.
GOOD MORNING
TEL ME IF THE TRUSS IS 10M DO I NEED AN ENGINEER TO DESIGN IT. AGAIN IF THE ROOM HIEGHT IS 3M TO THE CEILING DO I NEED AN ENGINEER
REGADS
EDGAR
Hi, i need sone advice please. I would like to enclose my patio with a louvered patio covering, would i need plans from an architect in order to do this?
Good day,
I have recently purchased a house with an asbestos roof (big 6 profile), I am playing with the idea of removing this roof in accordance with the asbestos regulations and sheeting the roof using aluminium roof sheeting (still not sure on the profile I prefer).
My question is, do I need to submit plans to do this? (I know I will need plans to go a roof tile due to the roof design and material weights)
Thanks for the advise.
Hi, I wouldl ike to know if anyone has an objective view with regards to a flat roof and a mono pitch roof… any help would be appreciated.
Thanks,
Deoni
Here is a table of minimum depths:
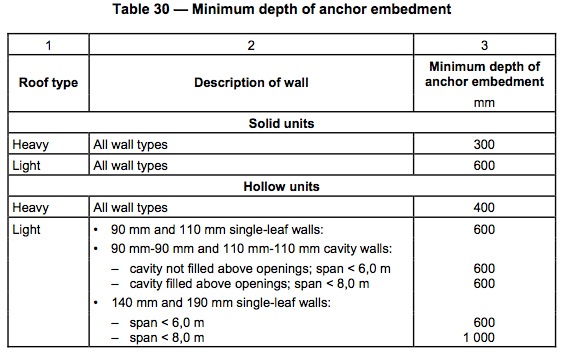
You should be ok with this as the regulations state that you do not need plans if you are changing the roof covering and changing it for a similar material. This is seen as maintenance and not an alteration. As asbestos is a no no then, so long as the roof truss configuration does not change then you will be fine.
A monopitch roof is built at an angle so rainwater will run off and will be easier to waterproof. A flat roof must have some runoff for water to flow off the roof but it must be properly sealed off otherwise there could problems.
Any roof has to have an engineers COC (Certificate of Compliance) and has to be designed by a “competent person”. Most truss manufacturers have suitably qualified roof designers and will supply you with the correct documentation.
• Message facility for questions and interview requests
Hi
I am doing a alteration to my house, and the architect has specified a slab, for a roof over the one area, this slab will have to go in under the exiting tiled roof, so I am limited at height the slab will need to be at. I see in the UK they use shutter board on trussing to create flat roofs, this is then covered with the torch on type of waterproofing.
So to save height , I want to know if three are any problems with creating a steel frame with Shutter board on top ,sealed with torch on waterproofing, insulation below then the ceiling.
I have not seen this system used in SA is there any reason why I should not do it this way?
Regards
Colin
Any system of building in SA has to have an Agrement certificate to show that it is a tested and approved method. If the system does not have this then a “competent person” (an architect or engineer, etc) will have to supply a report as to why this could be used and cite any sites in SA that may have safely used the same method in the past. Even though some methods of construction are used in the USA & the UK it does not mean that this meets our standards here in SA.
Good Morning
I am looking for some advise to a project i did about a year and half ago.
I build a corrugated roof over a clients bar area to give shade to the area it was build on four pillars I now have been told i needed to submit plans for this.
But when i started i was told that you do not need plans as you are not increasing the living area of the house or altering the shape of the house.
Please can someone explain what is the rules to this please
Hi, what are the type of bolt & washers recommended
for supporting the roof truss?
I am designing the re roofing of my braai room and the depth of the timber trusses is decreasing the height underneath the roof. I am considering a lightweight steel trussed alternative. Where can I find the SANS regulations dealing with steel roof trusses?
Hi
I have 2 queries.
1) My ceiling has sagged and insurance company has already informed me that the wrong nails were used. Normal steel nails have been used. They say according to building regulations the nails should be ridged. I have been searching the internet but cannot find any such SANS specification?
2) I am wanting to install Ceilings directly onto the brandering/purlins on the top of the truss (the ones that hold the tiles) so as to have exposed painted trusses in the room. However I see in SANS 10400-L:2011 Edition 3, that “cross top chord bracing” must be installed which will not allow me to do this. Is this the case or any ideas as I have seen roofs/ceilings build like this (exposed trusses)
I have an old home with concrete roof tiles. These are now old and brittle. Can I lay Chromodeck corrugated sheeting over the existing tiles ?
Hi John, I am sure that you can, but two things come to mind straight away, 1st how are you going to fix the sheeting onto brittle tiles, roof sheets normally will be nailed onto wooden purlins and or battens & 2nd the tiles are usually uneven so it will be difficult to get a nice flat roof laid. Possibly take all the tiles off first clean up the battens of protruding nails etc and then put your Chromodeck sheets down.
Cause and Effect?
I have a IBR (0.58) flat roof, that up till now i taught was built accordingly, to my surprise when obtaining quotes (for general maintenance) only one contractor informed me that my slope was not enough and that it was inadequate. I investigated his claims and have found them to be correct. My situation is that i purchased this house six months ago and had a roofing contractor requested by thee estate agent to inspect the quality and build of the roof, the same contractor i asked to quote me on performing general maintenance after purchase(not the one that informed me of the incorrect slope).
My comment/question?
Now i have a flat roof that is not built to regulation, what are my risks? (from local council, insurance companies and my home)
Thanks in advance.
If you are positive that the roof has not been built according to the NBR you can sue the contractor for damages and/or demand that he rebuilds according to the standards. Was the roof inspected by your local authority? It should have been. IBR can be laid as flat as 11 degrees.
There is nothing in Part L: Roofs of SANS 10400 about steel trusses, so I guess you would have to talk to a competent person who is qualified to specify what is required. Alternatively get hold of a company that makes steel trusses; chances are they will have an agrement certificate (for a non-standardised product). Here is one company – I know nothing about them, but you could give them a call for ideas.
This kind of detail is not specified in the NBR. The designer of your trusses must specify.
This is a puzzling one Stephen since you were obviously contracted to do a project and you clearly don’t know the building regs. That is disturbing to say the least. If you are working in the construction industry you should know what is required. Clearly you are at fault.
You have a right to ask for a reference in terms of where an SABS national standard states this. At very least they must tell you which SANS they are referring to. The implication – if it is according to the building regs – is that it is SANS 10400-L:2011. I can’t see anything in this that specifies any type of nail. The other thing to do is contact a distributor of the generic type of ceiling board used – e.g. plasterboard – and ask for information in terms of fixing.
Regarding exposed trusses, SANS 10243 provides guidance on the manufacture, erection and bracing of timber roof trusses. I am not an architect or engineer and cannot provide info on how to adapt an existing installation. You really do need to talk to a competent person – or someone that manufactures trusses.
Probably – check with your local authority … there is a possibility they won’t need plans.
Hi Penny, thanks for your reply.
I have asked my local municipality for one of their experienced roofing engineers to come out to my house and inspect my roof. Its a little bit late for me to now raise the issue of the roof with my estate agent at that time. Its unfortunate that i was informed of the incorrect pitch after i signed an offer to purchase. Now i am stuck with a risk on my asset.
Thanks
Hi Adriaan,
I live in a flat roof house (less than 1,0 degree slope), never had a leak in 35 year !
Only problem is if you neglect it, rust will accelerate because of the small slope,
Leaves and bad paint may cause water to stand in the real flat sections which will accelerate rust.
I am going to replace my roof shortly with the same specification and only change the screws to “Leak King”
Part L on roofing was published in 2011. When did it come into effect, and does it apply to structures erected before then? I have a house where one section of a roof was extended with a pitch of only 11 degrees and tiled, which does not comply with the regulations as I understand it.
This document was published in November 2011 – and so that’s when it came into effect (even though the Act changed in 2008). Part A of the NBR states “in general the National Building Regulations are not retroactive in application,” … so you need to check what the legislation said when your house was built. Or probably easier, check the approved plans to make sure that the roof was built according to plan. as far as the regs published in 1990 are concerned, tiled roofs had to be at least 17 deg – and if they were less than 26 deg they needed an underlay. If fibre-cement slates were used, the minimum slope had to be at least 10 deg – and if they were less than 17 deg they needed an underlay. Metal tiles could also be laid at 10 deg (with underlay). The minimum specs for corrugated sheeting of various kinds was 11 deg.
I have a 5 year old house. The roof has been constructed with treated poles and where the poles have been supported by the load bearing wall fine cracks have appeared below each pole….is this normal?????
I am impressed with the illustrations in the roofing instructions as shown. thanks
Thanks for the compliment Moses, always good to get these. Glad we could help. 😀
This often happens due to natural settling.
Hello
For someone like me who doesn’t know anything about roofing, this is very helpful. Thanks so much.
Good morning. I have a flat IBR double garage roof. During a massive storm the gutter got block with leaves. The roof is walled by approx half a meter. A pool knee deep formed on the roof. A steel beam that supported the roof collapsed. The insurance claims that the roof was suppose to withstand the weight. How much weight is a roof suppose to hold? Please help.
It’s not what weight a roof is supposed to be able to withstand, it depends whether the structure was built in compliance with the NBR. Gutters are expected to drain water rather than roofs being designed to support/hold water. If the gutter was blocked in a storm (and not because of lack of maintenance) my feeling is that the insurance company is liable.
Who is actually responsible for the specifications of the water proofing? Is it the engineer or the Architect?
hi , I recently bought a house , the house has 2 roofs which join in the middle the old house has a 12 degree slope and the added on section has a 24 degree slope , they join in the middle and run into a gutter I have tried everything to stop leaks which run into the house were these 2 joints meet please advise a way forward .
Hi, I had a fire in my thatch roof which the fire investigator says was started by something coming out the flue. The insurance company will not pay as there was no spark arrestor in the flue. There seems to be a lot of conflicting decisions as to whether a spark arrestor is compulsory or not. Please help.
IBR may be used at a minimum roof
pitch of 5˚ for sheet lengths up to 30 m.
A minimum of 7.5˚ is required for sheet
lengths greater than 30 m. For both
conditions an approved end-lap sealing
strip is recommended.
Hi, we bought a house with an extension the roof has no started to leak. We asked specifically before purchase if the extension was according to approved plans and was assured by the estate agent that it was. Now a year later the roof is leaking and according to roof inspection only 17 degrees (tile roof) so not built to code or to the approved plans….is there any way to hold the sellers or estate agent liable a year after purchase?
Report the agent to the Estate Agents Board and notify his/her superiors that you will be doing this. Since you asked the question, it will probably be considered a latent defect – i.e. they knew it hadn’t been done correctly. In that case you can hold them all liable.
Have a look at this article and also SANS 62305-3: Protection against Lightning
You need to contact someone who specialises in roofing.
Whoever the competent person is appointed to draw and submit plans and oversee the build. It could be an engineer or an architect.
Hi, the person that is assisting us with the building plans informed us that as of 01 July 2016 a new regulation/by law came into affect. If we want to build a granny flat or extend on our house, the roof of the new granny flat/extensions must be the same as the current house. Is this correct and where can i get more information on this. We are based in Parow, Cape Town.Thank you
If it’s a bylaw then the local authority (City of Cape Town) will be able to give you the relevant details. I can’t find anything relevant on their website.
Hi, what deal NHBRC say about roofing with concrete tile without under tile membrane?
Hi Meshak, Here is an extract from the SANS10400-PartL: Roofs
4.2.2.6 Undertile membranes shall be laid loose so that water can drain between rafters and shall be installed strictly in accordance with the manufacturer’s instructions where tiles, slates and shingles are laid
a) in roofs that have a pitch of less than 26°, or
b) in roofs that have a pitch of 45° or steeper, and
c) in those areas between the coastline and an imaginary line 30 km inland, parallel with the coastline, or the top of the escarpment or watershed of the first mountain range inland, if these are less than 30 km from the coastline.
NOTE The entire area of jurisdiction of any local authority, the area of which is cut by the line demarcating these coastal areas, is taken as falling within the coastal area.
I hope this answers your question.
Building a flatroof carport – with a slope of corse.
Placing the roof sheeting on beams – is that ok.
Another view by a carpenter – must have purlins.
A plan was submitted by an architect who agreed on the plan of utilising only beams.
Suggestions and ideas please, would be most welcome.
Hi Ramesh, If that is what the architect put on the plan then ask him again if this is correct as he is the person responsible. You can have a look at our book on “How to Build a Carport” we have a 50% discount at the moment – here: http://www.howtobooks.co.za/product/build-carport-easy-way/
I’m struggling with calculating the R-value and U-value of a Rib & block concrete slab roof. any advise out there?
Talk to a professional